How to use Input Capture in STM32
This guide explains how to use STM32 Input Capture with CubeMX and HAL libraries to accurately measure the frequency and pulse width of an input signal. You’ll learn how to set up STM32 timer input capture mode, configure interrupts, and use HAL_TIM_IC_CaptureCallback() to extract signal timing. This technique is useful for frequency counters, duty cycle measurement, or edge-based event detection in embedded applications.

Recommended Resources:
This tutorial uses the Timer to generate the PWM output, which is then measured using the input capture. The PWM output tutorial is already covered and you should take a look at it first.
This tutorial marks the 4th installment in our ongoing STM32 Timer Series. In this session, we will focus on one of the most practical and powerful features of the timer peripheral — the Input Capture mode.
The Input Capture functionality allows us to accurately measure key characteristics of an incoming signal, such as its frequency, period, and pulse width. By capturing the timer’s counter value at the precise moment an edge (rising or falling) occurs on the input pin, we can calculate these signal parameters with high precision.
Today’s tutorial will not only demonstrate how to configure the timer for Input Capture mode but will also provide a step-by-step explanation of the setup process, including CubeMX configuration, interrupt handling, and code implementation. By the end of this guide, you will have a solid understanding of how to use timers to perform accurate signal measurement in real-world applications.
VIDEO TUTORIAL
You can check the video to see the complete explanation and working of this project.
Check out the Video Below
Introducing the STM32 Input Capture mode
The Input Capture mode in STM32 timers is designed to precisely measure the characteristics of external signals, such as frequency, period, and pulse width. It works by capturing the timer’s counter value when a specific edge (rising or falling) is detected on the input pin. This captured value can then be processed to determine the time intervals between events, making it highly useful for signal analysis, frequency counting, and duty cycle measurement.
In this mode, the timer acts as a time base, while the input channel monitors incoming signals and records their timing characteristics without CPU intervention. Combined with interrupts or DMA, this feature allows for accurate and efficient signal measurement even at high speeds.
Some of its important features are:
- Accurate Frequency and Pulse Measurement – Captures precise time intervals between signal edges, enabling calculation of frequency, duty cycle, and pulse width.
- Edge Detection (Rising/Falling/Both) – Can be configured to trigger on rising edges, falling edges, or both, providing flexibility for different signal types.
- Hardware-Based Timing – Works directly with the timer hardware, reducing CPU overhead and improving measurement accuracy.
- Interrupt and DMA Support – Captured values can be processed via interrupts or transferred using DMA, allowing non-blocking and efficient operation in real-time systems.
What Is Input Capture in STM32 and When to Use It?
Input Capture allows the STM32 timer to record counter values at the moment a signal changes state (rising/falling edge). This is used to:
- Measure frequency or period of a signal
- Calculate pulse width or high/low time
- Decode signals like IR or PWM
- Monitor encoder or sensor outputs
Compared to polling or software delay, input capture provides hardware-level precision with minimal CPU load.
CubeMX CONFIGURATION
Clock Configuration
Below is the image showing the clock configuration for the project.
- Here we will use two timers, i.e Timer 1 for the PWM output and Timer 2 for the Input Capture
- Timer 1 is connected to the APB2, which is running at 180 MHz.
- Timer 2 is connected to the APB1, which is running at 90 MHz.
Input Capture Configuration
Below is the image showing the configuration of the TIMER 2 for Input Capture Mode.
- Enable the Input capture Direct Mode on channel 1.
- The Prescaler is set to 90, which will divide the APB2 clock by 90, making the Timer 2 clock = 1 MHz.
- I am leaving the ARR to 0xffffffff (Max for 32 bit Timer).
Also Enable the Interrupt for the TIM2. This allow the input Capture to trigger the interrupt, whenever the Rising / Falling Edge is detected.
PWM Output Configuration
The TIMER1 is configured to output a PWM signal. If you want to know more about PWM output, check out the tutorial PWM (Pulse Width Modulation) in STM32
How to Measure Frequency
In order to measure the Frequency of the input signal, we need to measure the time between the 2 rising edges, or between 2 falling edges.
- When the first Rising edge occurs, the counter value is recorded.
- Another counter value is recorded after the second rising edge occurs.
- Now the difference between these 2 counter values is calculated.
- This Difference in the counter values will give us the frequency.
STM32 HAL Code for Input Capture Frequency Measurement
This entire process is shown below.
#define TIMCLOCK 90000000
#define PRESCALAR 90
uint32_t IC_Val1 = 0;
uint32_t IC_Val2 = 0;
uint32_t Difference = 0;
int Is_First_Captured = 0;
/* Measure Frequency */
float frequency = 0;
void HAL_TIM_IC_CaptureCallback(TIM_HandleTypeDef *htim)
{
if (htim->Channel == HAL_TIM_ACTIVE_CHANNEL_1)
{
if (Is_First_Captured==0) // if the first rising edge is not captured
{
IC_Val1 = HAL_TIM_ReadCapturedValue(htim, TIM_CHANNEL_1); // read the first value
Is_First_Captured = 1; // set the first captured as true
}
else // If the first rising edge is captured, now we will capture the second edge
{
IC_Val2 = HAL_TIM_ReadCapturedValue(htim, TIM_CHANNEL_1); // read second value
if (IC_Val2 > IC_Val1)
{
Difference = IC_Val2-IC_Val1;
}
else if (IC_Val1 > IC_Val2)
{
Difference = (0xffffffff - IC_Val1) + IC_Val2;
}
float refClock = TIMCLOCK/(PRESCALAR);
frequency = refClock/Difference;
__HAL_TIM_SET_COUNTER(htim, 0); // reset the counter
Is_First_Captured = 0; // set it back to false
}
}
}
- The above interrupt callback function is called whenever the Rising edge is detected.
- When called first time, Is_First_Captured was 0 so the hence the IC_Val1 will be recorded.
- When called after the second rising edge, the Is_First_Captured is 1 now so IC_Val2 will be recorded.
- We will calculate the Difference between the 2 IC values.
- Reference clock is calculated based on the setup we have done for our timer.
- Frequency is equal to the (Reference clock / Difference). This is because the counter value depends on the Timer clock.
In the main function, we have to start the TIMER in the Input capture interrupt mode.
I am also starting the Timer 1 in the PWM mode, so to provide the signal for the Timer2.
TIM1->CCR1 = 50;
HAL_TIM_PWM_Start(&htim1, TIM_CHANNEL_1);
HAL_TIM_IC_Start_IT(&htim2, TIM_CHANNEL_1);
Result
Below is the image showing the output of the above code.
How to Measure Pulse Width
CubeMX Configuration
In order to measure the Pulse width, the interrupt should trigger on both the edges of the incoming signal. To do so, we need to modify the CubeMX as shown below.
As you can see in the image above, I have switched the Polarity to both the edges. This will make the interrupt to trigger for both the edges of the incoming signal.
Also Enable the Interrupt for the TIM2. This allow the input Capture to trigger the interrupt, whenever the Rising / Falling Edge is detected.
STM32 HAL Code to measure Pulse Width
- When the first rising edge occurs, The counter value is stored in the ICVal1.
- The next interrupt will occur at the falling edge, and the counter value is stored in the ICVal2.
- The Pulse width can be calculated using this counter value.
The process for the same is shown below
/* Measure Width */
uint32_t usWidth = 0;
void HAL_TIM_IC_CaptureCallback(TIM_HandleTypeDef *htim)
{
if (htim->Channel == HAL_TIM_ACTIVE_CHANNEL_1) // if the interrupt source is channel1
{
if (Is_First_Captured==0) // if the first value is not captured
{
IC_Val1 = HAL_TIM_ReadCapturedValue(htim, TIM_CHANNEL_1); // read the first value
Is_First_Captured = 1; // set the first captured as true
}
else // if the first is already captured
{
IC_Val2 = HAL_TIM_ReadCapturedValue(htim, TIM_CHANNEL_1); // read second value
if (IC_Val2 > IC_Val1)
{
Difference = IC_Val2-IC_Val1;
}
else if (IC_Val1 > IC_Val2)
{
Difference = (0xffffffff - IC_Val1) + IC_Val2;
}
float refClock = TIMCLOCK/(PRESCALAR);
float mFactor = 1000000/refClock;
usWidth = Difference*mFactor;
__HAL_TIM_SET_COUNTER(htim, 0); // reset the counter
Is_First_Captured = 0; // set it back to false
}
}
}
- The above callback function is called when either the Rising or Falling edge is detected.
- When called for the rising edge, Is_First_Captured was 0 so the hence the IC_Val1 will be recorded.
- When called for the falling edge, the Is_First_Captured is 1 now so IC_Val2 will be recorded.
- We will then calculate the Difference between the 2 values.
- This difference is the time for which the Pulse is high, and this time will depend on the timer configuration.
- To measure this time in microseconds, we have to use the reference clock.
- Reference clock is calculated based on the setup we have done for our timer.
- And finally, the usWidth will be calculated.
Understanding HAL_TIM_IC_CaptureCallback() in STM32
This HAL callback function is triggered when the configured edge (rising/falling/both) is detected on the timer input pin.
- Used to store the counter value at each detected edge
- Helps track timing between two edges
- You can calculate frequency, pulse duration, or even infer signal logic states
Example use cases:
- First edge → store value in IC_Val1
- Second edge → store IC_Val2, calculate difference
- Reset counter and repeat
Using STM32 input capture with HAL is a clean, reliable way to measure real-world signals. Whether you’re counting pulses, reading sensor timings, or decoding waveform data, this method provides hardware-accurate results with minimal code. With the help of HAL_TIM_IC_CaptureCallback(), you can monitor frequency and duty cycle efficiently using interrupts.
PROJECT DOWNLOAD
Info
You can help with the development by DONATING Below.
To download the project, click the DOWNLOAD button.
You might also like
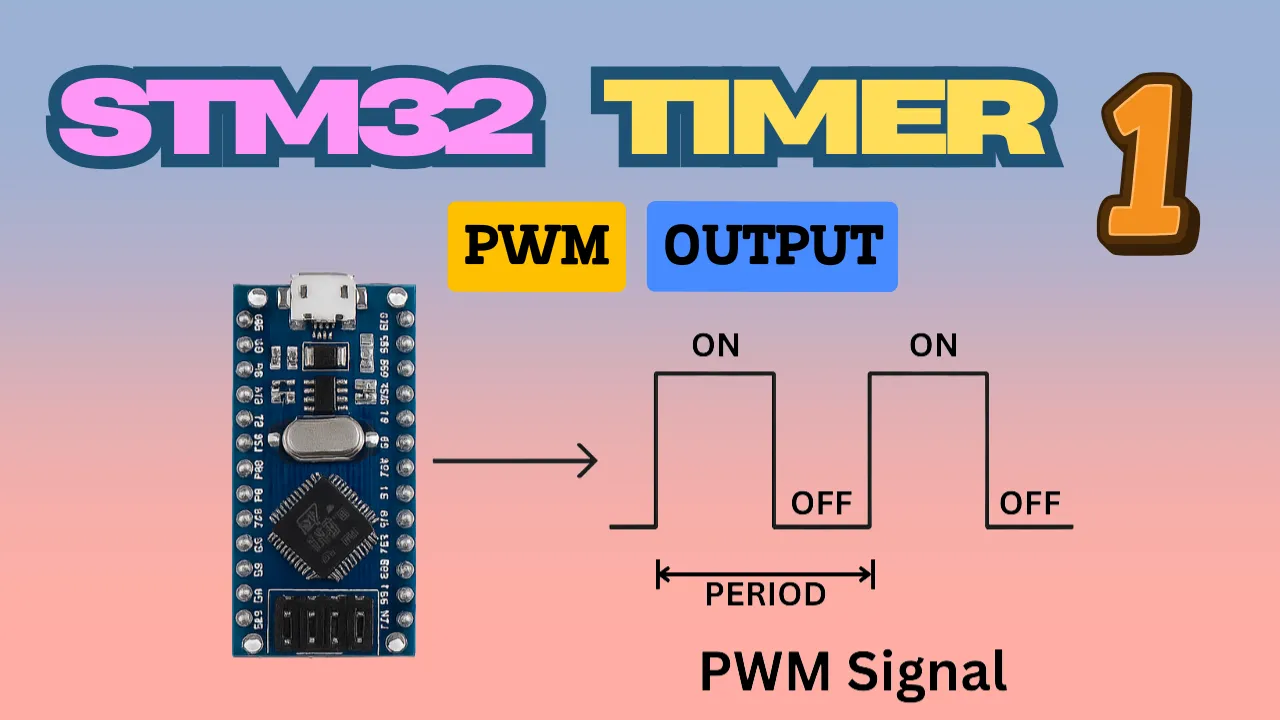
PWM in STM32 Using Timer – Step-by-Step Guide with Code Examples
Support Us by Disabling Adblock
We rely on ad revenue to keep Controllerstech free and regularly updated. If you enjoy the content and find it helpful, please consider whitelisting our website in your ad blocker.
We promise to keep ads minimal and non-intrusive.
Thank you for your support! 💙
Hii Good afternoon,
I am using STM32F401re nucleo board, for measure the input capture frequency
but in that i am seeing frequency rising edge is not detect by
“IC_Val1 = HAL_TIM_ReadCapturedValue(htim1, TIM_CHANNEL_1);”
this function so value remain 0 as per this code.
please suggest what i should do?
Or can you suggest any other function to read the rising edge from register in Input Capture
my function is
void CaptureCallback(TIM_HandleTypeDef *htim1)
{
if (htim1->Channel == HAL_TIM_ACTIVE_CHANNEL_CLEARED)
{
if (Is_First_Captured==0) // if the first rising edge is not captured
{
IC_Val1 = HAL_TIM_ReadCapturedValue(htim1, TIM_CHANNEL_1); // read the first value
Is_First_Captured = 1; // set the first captured as true
}
else // If the first rising edge is captured, now we will capture the second edge
{
IC_Val2 = HAL_TIM_ReadCapturedValue(htim1, TIM_CHANNEL_1); // read second value
if (IC_Val2 > IC_Val1)
{
Difference = IC_Val2-IC_Val1;
}
else if (IC_Val1 > IC_Val2)
{
Difference = (0xffffffff – IC_Val1) + IC_Val2;
}
else if (IC_Val1 == IC_Val2)
{
Difference = IC_Val2;
}
float refClock = TIMCLOCK/(PRESCALAR);
frequency = refClock/Difference;
__HAL_TIM_SET_COUNTER(htim1, 0); // reset the counter to start
Is_First_Captured = 0; // set it back to false
}
}
}
uint32_t HAL_TIM_ReadCapturedValue(TIM_HandleTypeDef *htim, uint32_t Channel)
{
uint32_t tmpreg = 0U;
switch (Channel)
{
case TIM_CHANNEL_1:
{
/* Check the parameters */
assert_param(IS_TIM_CC1_INSTANCE(htim->Instance));
/* Return the capture 1 value */
tmpreg = htim->Instance->CCR1;
break;
}
case TIM_CHANNEL_2:
{
/* Check the parameters */
assert_param(IS_TIM_CC2_INSTANCE(htim->Instance));
/* Return the capture 2 value */
tmpreg = htim->Instance->CCR2;
break;
}
case TIM_CHANNEL_3:
{
/* Check the parameters */
assert_param(IS_TIM_CC3_INSTANCE(htim->Instance));
/* Return the capture 3 value */
tmpreg = htim->Instance->CCR3;
break;
}
case TIM_CHANNEL_4:
{
/* Check the parameters */
assert_param(IS_TIM_CC4_INSTANCE(htim->Instance));
/* Return the capture 4 value */
tmpreg = htim->Instance->CCR4;
break;
}
default:
break;
}
return tmpreg;
}
Here are both functions for your reference, Please suggest what changes are need.
Thank you.
Hi
When you measure the width- because trigger is both edges, how do you know that the first interrupt is the rising? if duty cycle is NOT 50% as here , if the interrupt is will be due the falling you will measure the low width od the pulse.You have to check the cause to the interrrupt is falling or rising and calculate the 2 width of the signal – the high part and the low part.Is it? Can I know what was the edge while enter the interrupt?
incrivel artigo sobre stm32
can i have your tutorials in just register level based , using HAL and all makes it very convoluted and i guess its not the best practise to do so .
Thank you so much.
I have learned from you.
It is very clear and understandable even for the beginners.
i initially started with this technique, but found that with this model that the interrupts are proportional to the frequency being measured, and you quickly saturate the MPU with interrupts (as you noticed) leaving you with nothing but an interrupt generation machine as the freq of the signal to be measured goes up, with no cycles left for anything else. In my case I am trying to measure the freq of an external input. what i did was use one timer to provide/manage the “gate” for another timer, and CLOCK the second timer with the external freq to be measured. now the interrupt rate is independent of my “unknown” frequency, and i am readily able to measure frequencies over 30mhz, with a gate frequency of 250ms (created by the first timer by linking the second to the first timer). connect the input being measured to the external clock source of the second timer (note- not all STM32 timers allow external clock source). In my case, T3 gates T2, T3 is setup with MasterslaveOutTrig = TRG0_OC1REF and MasterSlaveMode enabled, T2 is setup with CLKSRC=ETRMODE2 and SLAVEMODE=SLAVEMODE_GATED ITR2. in the T3 PeriodElapsed callback, read T2’s counter directly as the frequency
I think I met your issue that jam the interrupts… and agree that alternative is best to measure some high speed tachometer PWM inputs.
unfortunately, I cant fully get your solution in your message.
Hi man, please how do I measure the speed of a bldc motor by capturing the hall sensor signals (H1,H2,H3) on an STM32. Do you mind refering me to a video or link if you have one?
Hi man, please how do I measure the speed of a bldc motor by capturing the hall sensor signals (H1,H2,H3)
Coming from Measure input frequency using stm32 article where the main issue was code getting stuck in the frequency counter loop.
I just wanted to share how I configured my project to get this working in STM32CubeIDE v1.4.0 and STM32F103C8T6 (aka blue pill) board.
I set my clock configuration as follows:
By the same token I set my parameters as:
Code wise on the frequncy calculation changed:
According to the calculation lowest measureable frequnechy is 549 Hz.
What options do I have if I want to measure signals at 200 Hz? Adjust APB1 Prescaler from “/4” to “/16” seem to do the trick but is the right way to do it?
yes you did it right. As per with this code, you need to reduce the sysclock inorder to measure the lower frequencies
Helo
I tried this code and working fine . But when frequency increase , after about 36kHz the main loop stops to work . When decrease the frequency , main loop begins to work again . But frequency measurement still fine even main loop stop. Do you have any advice ?
what you mean main loop stops ?
Inan want to say …. what ever he writes in while loop thats not working when frequency increases …. it is because when frequency increase callback function interrupts increases with it and cpu do not get extra time to perform while loop code out of interrupt … when decrease frequency cpu get out of interrupt for some time and get some extra time to run while loop code also …. if there is any way to fix it im also interested to know
i don’t think it will work. One way you could try is instead of putting the entire code in the callback, just use some flag, and put the code in the while loop.
maybe that could work
I’m facing a similar problem, I can read up to 115Khz, but anything high causes my stm32 to stop work properly, I’m also using serial com and the board stop to receive RX but still send TX.
Well that may be because the uart baud rate could be 115200.
i saw that if i use internal crystal and low working frequency(16 Mhz) at the cubemx , main loop stop to work at high frequency measures like 36 khz . I used external crystal and set max speed(168 Mhz) . now it is working perfect. thanks
thats great 😀😀 … always remember to put top gear 🚀🚀of ur hardware before exicute anything 😁😁😁
aswdf
Thanks for this example, works fine.
Thanks, this tutorial was super useful to get the capture inputs working. Showing both the code and cube mx configuration did the trick.
Hello! Thank you for your tutorial! Could I ask what to do if the rising edge will come in two channels at the same time?