STM32 ADC Multi‑Channel using Circular DMA Mode
Explore STM32 ADC multi‑channel setup with DMA in circular mode. This tutorial includes Step‑by‑step CubeMX configuration, HAL C code, and STM32F1/F4/H7 examples. The project is available to download at the end of the post.
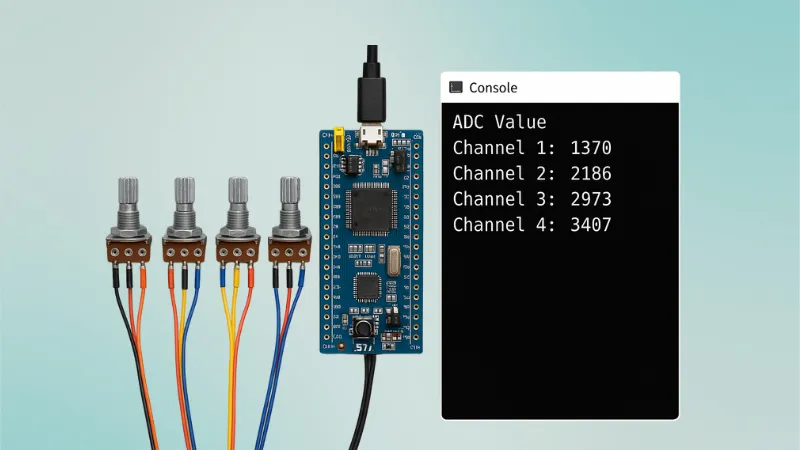
Recommended Resources:
This is the 4th tutorial in the STM32 ADC series. In the previous tutorials we covered how to configure the ADC in STM32 F1, F4 and F7 series and how to use it in the single channel polling, interrupt and DMA modes to read the potentiometer data. We have also covered the Multiple channels in DMA Normal Mode.
You should take a look at the following tutorials before continuing here:
- STM32 ADC Single Channel Polling Mode
- STM32 ADC Single‑Channel Interrupt & DMA Modes
- STM32 ADC Multi-Channel DMA (Normal Mode)
VIDEO TUTORIAL
You can check the video to see the complete explanation and working of this project.
Check out the Video Below
Introducing STM32 ADC Peripheral
The Analog-to-Digital Converter (ADC) in STM32 microcontrollers is a powerful peripheral that allows the conversion of analog input signals into digital values. This capability enables STM32 devices to interface seamlessly with real-world sensors and analog inputs, such as temperature sensors, light sensors, potentiometers, and more. The ADC module is highly configurable and supports a range of resolutions and modes, making it suitable for both basic and advanced embedded applications.
Whether you’re developing a battery-powered IoT device or a high-speed data acquisition system, the STM32 ADC provides flexible configuration options, precision control, and efficient performance.
Here are some important features of STM32 ADC:
- Multi-Channel Support – Capable of reading from multiple analog inputs using internal channel scanning, reducing the need for external hardware.
- High Resolution Options – Offers selectable resolutions (6-, 8-, 10-, or 12-bit), allowing a balance between accuracy and conversion speed.
- Multiple Conversion Modes – Supports single, continuous, scan, and discontinuous modes to suit different application needs.
- Flexible Triggering – Conversion can be started via software or automatically triggered by hardware events like timers or external interrupts.
- Low Power Consumption – Designed with power-saving features, ideal for energy-efficient and battery-operated systems.
CONFIGURATION
We will connect 4 potentiometers to the 4 channels of the same ADC. As I mentioned we will setup the DMA in Circular mode, so it will continue to transfer the data from ADC channels.
We will see the available configuration for all three MCUs, F103C8, F446RE and H750VB.
F103C8 Configuration
We will start with the F103C8. Below is the image showing the configuration for the it.
I have enabled 4 channels of the ADC1. This is where the 4 potentiometers will be connected to.
Since we are using 4 different Channels of ADC1, set the Number of Conversions (under ADC_Regular_ConversionMode) to 4. This will automatically enable the Scan Conversion Mode, which is necessary in case of Multiple Channels.
You can configure the Rank and Sampling Time for each channel. The Rank determines the sequence in which the channels will be converted.
The Continuous Conversion Mode should be Enabled. Doing so will make sure the ADC start another conversion for all the channels automatically. This way the ADC will keep converting the data continuously.
In the DMA section, add the DMA request for the ADC1. Also make sure that the DMA is configured in the Circular Mode. In this mode the DMA will transfer the data continuously.
The F103C8 has 12 bit ADC resolution by default and we don’t have the option to configure it. Therefore the data width for the DMA must be set to Half-Word (16 bits).
F446RE Configuration
Below is the image showing the configuration for the F446RE.
I have enabled 4 channels of the ADC1. This is where the 4 potentiometers will be connected to.
Since we are using 4 different Channels of ADC1, set the Number of Conversions (under ADC_Regular_ConversionMode) to 4. This will automatically enable the Scan Conversion Mode, which is necessary in case of Multiple Channels.
You can configure the Rank and Sampling Time for each channel. The Rank determines the sequence in which the channels will be converted.
The Continuous Conversion Mode should be Enabled. Doing so will make sure the ADC start another conversion for all the channels automatically. This way the ADC will keep converting the data continuously.
The DMA Continuous Request must also be Enabled. This is to make sure that the DMA requests the data continuously from the ADC. This mode should be kept Enabled while using the DMA in Circular mode.
The End of Conversion Selection should be set at the end of all the conversions. Doing this will make sure that the Conversion complete interrupt in only triggered when all the 4 channels (one complete sequence) have been converted.
In the DMA section, add the DMA request for the ADC1. Also make sure that the DMA is configured in the Circular Mode. In this mode the DMA will transfer the data continuously. Set the data width as per the ADC Resolution. I have configured the ADC with 12bits resolution, therefore the data width is set to half word (16bits).
H750VB Configuration
Below is the image showing the configuration for the H750VB.
I have enabled 4 channels of the ADC1. This is where the 4 potentiometers will be connected to.
Since we are using 4 different Channels of ADC1, set the Number of Conversions (under ADC_Regular_ConversionMode) to 4. This will automatically enable the Scan Conversion Mode, which is necessary in case of Multiple Channels.
You can configure the Rank and Sampling Time for each channel. The Rank determines the sequence in which the channels will be converted.
The Continuous Conversion Mode should be Enabled. Doing so will make sure the ADC start another conversion for all the channels automatically. This way the ADC will keep converting the data continuously.
The Conversion Data Management Mode should be set to DMA Circular. This is to make sure that the DMA does requests the data continuously from the ADC. This mode should be used while using the DMA in Circular mode.
The End of Conversion Selection should be set at the end of sequence of conversion. Doing this will make sure that the Conversion complete interrupt in only triggered when all the 4 channels (one complete sequence) have been converted.
In the DMA section, add the DMA request for the ADC1. Also make sure that the DMA is configured in the Circular Mode. In this mode the DMA will transfer the data continuously. I have configured the ADC resolution of 16bits, therefore the data width is set to Half-Word (16bits).
Cortex M7 Related
In this section we will cover the configuration and code exclusively needed for the cortex M7 devices.
We know that as per ST’s recommendation, we should use the Instruction and Data cache to improve the system performance. But if the cache are enabled, the DMA will always have the cache coherency issue. This is why we will use the Memory Processing Unit (MPU) of the cortex M7 to deal with the cache coherency.
Below is the image showing the MPU configuration in the cortex M7 Devices.
As you can see in the image above, I have enabled both Instruction and Data Cache (ICache & DCache).
We also need to enable the MPU in the MPU_PRIVILEGED_DEFAULT mode. Here I am choosing the Base Address region 0x30000000, this is the region for the RAM_D2 and we will relocate our buffer in this region.
- Here I have selected the 32 Bytes region, since it’s the least size available. The ADC Buffer is going to be 20 bytes in size.
- The rest of the configuration is to set the region as non-cacheable region. This would prevent the cache coherency issue between the CPU and the DMA.
In the main file, we need to relocate the ADC_VAL array to the RAM_D2 Region, 0x30000000. We can do this by using the section attribute as shown below.
__attribute__((section(".adcarray"))) uint16_t ADC_VAL[4];
Here I am relocating the ADC_VAL array to the section “.adcarray“. The section (.adcarray) will be defined in the flash script file as shown below.
.mysection (NOLOAD):
{
. = ABSOLUTE(0x30000000);
*(.adcarray)
} >RAM_D2
As you can see above, the section (.adcarray) is linked to the region RAM_D2 (0x30000000).
The rest of the code remains the same as we used in the DMA section.
WIRING DIAGRAM
Below is the image showing the connection between the potentiometers and the H750.
As you can see in the image above, the 4 potentiometers are connected to the 4 pins of the MCU. These 4 pins represents 4 channels of the ADC. The potentiometers are connected to the 3.3V from the MCU.
THE CODE
The code will remain the same for all the STM32 MCUs. If there are any changes, I will specify in this section itself.
Definitions
Let’s define some variables, which we will use in the main function later.
uint16_t ADC_VAL[4];
//__attribute__((section(".adcarray"))) uint16_t ADC_VAL[4]; // cortex M7 only
int count = 0;
ADC_VAL is an array of 4 elements of 16 bit in size. We will use this array to store the converted ADC Value. Even if you are using 10bits, 12bits or 14bits resolution the ADC_VAL will still be defined as a 16 bit variable.
The count variable will keep track if the rest of the while loop is working fine.
The main function
Below is the main function.
int main ()
{
....
....
HAL_ADC_Start_DMA(&hadc1, ADC_VAL, 4);
while (1)
{
count++;
HAL_Delay(500);
}
}
Inside the main function, we will start the ADC in the DMA mode. The parameter ADC_VAL is the array where we want to store the converted data, and 4 is the number of conversions we want the DMA to transfer.
Once the DMA finishes the transfer of the converted data from all the channels, an interrupt will trigger and the Conversion complete callback will be called. The DMA will again restart the transfer request from the ADC, and this process will continue forever.
Conversion Complete Callback
void HAL_ADC_ConvCpltCallback(ADC_HandleTypeDef *hadc)
{
// Process the data
}
Inside the callback we can process the received data or set another variable. This variable indicate that the DMA has finished the transfer and we can now process the data anywhere in the code.
In circular mode, the DMA will continue transferring the data for all the channels. Therefore we do not need to start the ADC in DMA mode again.
PROJECT DOWNLOAD
Info
You can help with the development by DONATING Below.
To download the project, click the DOWNLOAD button.
Similar Posts ...
Support Us by Disabling Adblock
We rely on ad revenue to keep Controllerstech free and regularly updated. If you enjoy the content and find it helpful, please consider whitelisting our website in your ad blocker.
We promise to keep ads minimal and non-intrusive.
Thank you for your support! 💙
Hello, I’m trying to use the STM32H753ZI nucleo board with two ADG732 mux.. one mux connected to ADC1_INP2 and one mux connected to ADC1_INP3 for a total of 64 input channels. I need to scan both ADC channels, step mux address, and repeat, filling a ring buffer[64]. I put my DMA buffer in RAM_D3 as this area is a non-cacheable area, so I didnt need to mess with MPU/cache. However, its not working as intended. I can either get all 64 buffer spots to continuously show channel0 of their respective mux (buffer[0,2,4,6,8…] showing mux1 channel0 and buffer[1,3,5,7,9….] showing mux2 channel0), or they cycle through all 32 channels of their respective mux (buffer[0,2,4,6,8…] cycling through mux1 channel0,2,4,6,8… and buffer[1,3,5,7,9…] cycling through mux2 channel1,3,5,7,9…). I have not been able to get it to fill the buffer correctly (each buffer spot remains with its intended channel i.e. buffer[0] = mux1 channel0, buffer[1] = mux2 channel0, buffer[2] = mux1 channel1, and so on. Can you please help?
Hi, I am using same setup and code you have suggested for 446RE but when there is any change in one channel then it is affecting others as well. I am using sampling time for all 480 cycles. Any suggestions?
Awesome